The Science Behind Porosity: A Comprehensive Overview for Welders and Fabricators
Comprehending the complex systems behind porosity in welding is important for welders and fabricators aiming for remarkable craftsmanship. As metalworkers look into the depths of this sensation, they reveal a world controlled by various elements that influence the formation of these small gaps within welds. From the structure of the base products to the ins and outs of the welding procedure itself, a wide range of variables conspire to either worsen or ease the presence of porosity. In this extensive guide, we will decipher the science behind porosity, exploring its effects on weld top quality and unveiling progressed methods for its control. Join us on this trip through the microcosm of welding blemishes, where precision meets understanding in the pursuit of flawless welds.
Understanding Porosity in Welding
FIRST SENTENCE:
Examination of porosity in welding exposes vital understandings right into the honesty and top quality of the weld joint. Porosity, identified by the presence of tooth cavities or spaces within the weld metal, is a typical worry in welding procedures. These gaps, otherwise effectively resolved, can endanger the architectural honesty and mechanical homes of the weld, leading to possible failings in the completed product.
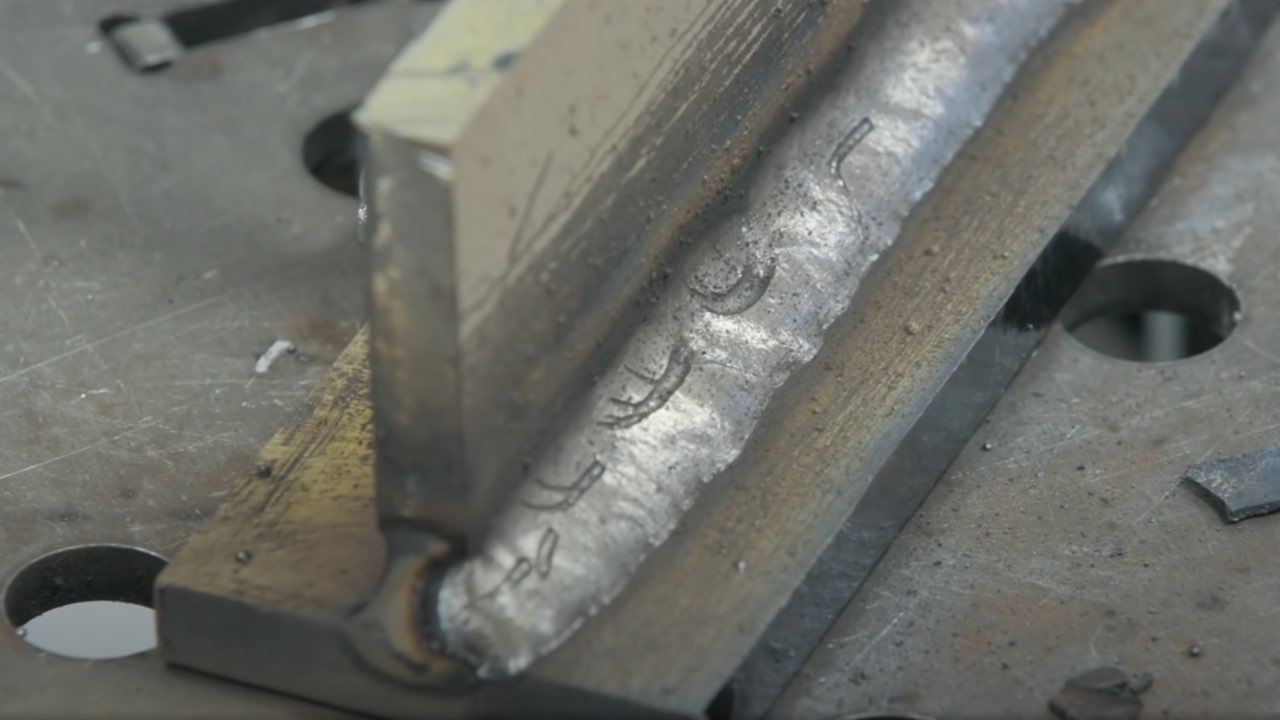
To identify and quantify porosity, non-destructive screening approaches such as ultrasonic testing or X-ray assessment are usually used. These methods permit the recognition of internal flaws without endangering the integrity of the weld. By evaluating the size, form, and circulation of porosity within a weld, welders can make educated decisions to enhance their welding procedures and accomplish sounder weld joints.

Variables Influencing Porosity Formation
The event of porosity in welding is influenced by a myriad of factors, ranging from gas securing performance to the intricacies of welding specification setups. One crucial factor adding to porosity development is poor gas securing. When the shielding gas, usually argon or CO2, is not properly covering the weld swimming pool, climatic gases like oxygen and nitrogen can contaminate the liquified metal, causing porosity. In addition, the sanitation of the base materials plays a significant role. Impurities such as rust, oil, or wetness can evaporate throughout welding, developing gas pockets within the weld. Welding parameters, consisting of voltage, current, travel rate, and electrode kind, likewise influence porosity development. Utilizing incorrect setups can generate too much spatter or warm input, which consequently can result in porosity. The welding strategy utilized, such as gas steel arc welding (GMAW) or secured steel arc welding (SMAW), Go Here can influence porosity development due to variations in heat circulation and gas insurance coverage. Comprehending and regulating these aspects are necessary for decreasing porosity in welding procedures.
Effects of Porosity on Weld High Quality
The presence of porosity also weakens the weld's resistance to rust, as the entraped air or gases within the voids can respond with the surrounding atmosphere, leading to destruction over time. Additionally, porosity can hinder the weld's ability to hold up against pressure or effect, more threatening the total quality and integrity of the bonded structure. In essential applications such as aerospace, automobile, or architectural building and constructions, where safety and security and longevity are critical, the harmful results of porosity on weld quality can have extreme effects, highlighting the value of decreasing porosity with correct welding methods and procedures.
Strategies to Reduce Porosity
Furthermore, using the proper welding parameters, such as the appropriate voltage, existing, and travel speed, is important in stopping porosity. Maintaining a regular arc size and angle during welding additionally helps lower the likelihood of porosity.

In addition, selecting the ideal protecting gas and preserving appropriate gas circulation prices are crucial in reducing porosity. Making use of the appropriate welding method, such as back-stepping or employing a weaving activity, can additionally aid disperse warmth equally and reduce the chances of More Bonuses porosity formation. Ensuring proper air flow in the welding setting to get rid of any type of prospective resources of contamination is essential for attaining porosity-free welds. By implementing these strategies, welders can efficiently reduce porosity and generate premium welded joints.
Advanced Solutions for Porosity Control
Carrying out innovative technologies and innovative methods plays a critical duty in attaining exceptional control over porosity in welding procedures. One innovative remedy is using sophisticated gas mixtures. Protecting gases like helium or a mix of argon and hydrogen can help in reducing porosity by supplying far better arc security and boosted gas insurance coverage. Additionally, using advanced welding methods such as pulsed MIG welding or changed environment welding can likewise aid alleviate porosity concerns.
An additional advanced service includes using sophisticated welding devices. For circumstances, utilizing tools with integrated features like waveform control and sophisticated source of power can enhance weld quality and decrease porosity threats. Furthermore, the implementation of automated welding systems with exact control over parameters can dramatically minimize porosity flaws.
Additionally, integrating sophisticated tracking and examination link modern technologies such as real-time X-ray imaging or automated ultrasonic testing can help in identifying porosity early in the welding process, enabling immediate restorative activities. Overall, incorporating these sophisticated remedies can substantially enhance porosity control and enhance the general top quality of bonded parts.
Conclusion
In verdict, recognizing the scientific research behind porosity in welding is crucial for welders and producers to create high-grade welds - What is Porosity. Advanced services for porosity control can even more enhance the welding procedure and make certain a strong and reliable weld.
Comments on “What is Porosity in Welding: Understanding Its Causes and Enhancing Your Abilities”